Threaded Inserts for Plastics
When inserted into plastic material, metal threaded inserts increase the strength and durability of the threaded part of the component. These qualities are especially useful in applications requiring frequent assembly and disassembly for service and repair operations.
Types of Inserts for Plastics
There are many types of threaded inserts used for plastic materials. Each type features different design and construction characteristics, which makes them suited for certain applications.
Molded-In Inserts
Molded-in inserts are placed in plastic components during the part molding process. As these inserts come pre-installed, they do not require installation equipment or a separate installation step when used, reducing the overall costs of time, labor, and equipment. They are available in thru-threaded (open on both ends) or blind-threaded (closed on one end) models and are suitable for use with thermosets and thermoplastics.
Threaded Studs
Threaded studs are typically employed for specialized applications, such as reducing production costs, use in electrical and electronic devices, or as an alternative to self-tapping and removable screws. These inserts usually feature knurls in the inserted end to hold it in place within the component and threaded or non-threaded exposed ends depending on the intended application.
Press-In Inserts
As suggested by their name, press-in inserts are inserted by pressing them into pre-molded or pre-drilled holes. Installation of these inserts can occur at any time during the production process and can be performed by any standard press. They serve as an alternative to molded-in and heat staking inserts.
Compression Limiter
Compression limiters are inserts that do not have threads. Their primary function is to strengthen the plastic component, allowing it to withstand compressive forces. They are available in a variety of forms, including flange-head, symmetrical, full diamond knurl, and non-knurled symmetrical, and are installed by ultrasonic, heat staking, and molded-in methods.
Inserts for Plastic and Stainless Steel
Inserts designed for plastic and stainless steel are suitable for straight hole and thin-walled applications as the walls of these components experience less stress. The design of these inserts features knurls and undercuts to ensure better displacement of materials and reduces cycle times.
Inserts for Hard Plastics
Inserts designed for hard plastics and thermosets provide adequate holding strength within components without the use of ultrasonic of heat installation methods. The pilot end of these inserts allows for quick alignment, while the helical knurls provide superior torque-out resistance.
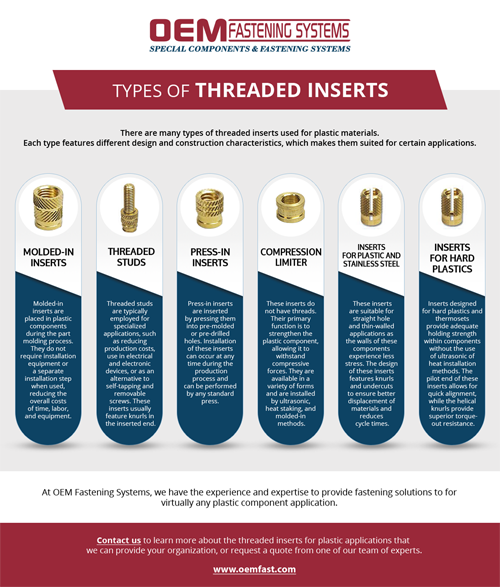
Ways to Install Threaded Inserts
Another way of classifying threaded inserts is by their installation method. Some of the typical installation methods for plastic threaded inserts include:
Installing Heat Staking Inserts
The heat staking installation method begins with a pre-drilled or pre-formed hole in the plastic component, which is slightly smaller than the OD of the insert. These inserts may be straight or tapered (allowing for easier and quicker installation), which are heated by a thermal press. As they are pressed into the component, they melt a portion of the surrounding material, which forms a firm bond after re-hardening. This process works best with thermoplastics and exhibits high performance at a lower installation cost.
Installing Ultrasonic Assisted Inserts
Similar to heat staking, this method also begins with a pre-drilled or pre-formed hole but replaces the heat press with an ultrasonic press. The ultrasonic installation process produces vibrations that melt the plastic and press the insert into place and requires precise control to minimize the size of the process-affected zone. As the process is relatively loud and hard to automate, it is generally only used by shops that already perform ultrasonic welding. It demonstrates high overall performance and best suits thermoplastics.
Installing Molded-In Inserts
The installation of this type of insert occurs during the molding process of the plastic component, encapsulating it into the manufactured part. By placing molded-in inserts into the component during the production process, they minimize the number of manufacturing steps required and reduce the total production cost. This method also provides greater assurance against torque and pullout damage.
Installing Cold Pressed-In Inserts
The easiest and most cost-effective installation method requires installing inserts by pressing them into pre-drilled or pre-formed holes. Pressed-in inserts are installed at any point during or after the production process and do not require heat or ultrasonic equipment for their installation. It is generally employed for thermoset materials.
Threaded Insert Applications
Threaded inserts are used in the manufacture of thermoset and thermoplastic components across a broad range of industries, including:
- Aerospace
- Automotive
- Defense
- Electronics (smartphones and handheld devices)
- General manufacturing
- Medical
- Recreational equipment manufacturing
- Transportation
Request Your Custom Fastening Solution Today
At OEM Fastening Systems, we have the experience and expertise to provide fastening solutions to for virtually any plastic component application. We are a leading distributor of threaded inserts, meeting and exceeding industry demands and the needs of our clients. Our facilities provide a broad range of inserts available in various sizes, shapes, and installation methods according to the requirements of the fastening application.
Contact us to learn more about the threaded inserts for plastic applications that we can provide your organization, or request a quote from one of our team of experts.